Analysis of advantages and recommended applications of aluminum silicate series products
Release Time:
2021-09-15
-
Performance analysis of various products in the aluminum silicate series
-
SIPERNAT ® 820 A FAQs
Contents of this article
For product grades that are not fully marked in the chart below, please read the following notes:
820 A = SIPERNAT ® 820 A
830 = SIPERNAT ® 830
833 = SIPERNAT ® 833
835 = SIPERNAT ® 835
OK 412 = ACEMATT ® OK 412
Members of the aluminum silicate family make a concentrated appearance
As a multifunctional filler, SIPERNAT ® 820 A has always been Evonik's star product in ink applications.
In addition to the star product SIPERNAT ® 820 A, the aluminum silicate series also includes other products such as SIPERNAT ® 830, SIPERNAT ® 833 and SIPERNAT ® 835.
All aluminum silicate products have the characteristics of improving white ink coverage, improving ink anti-blocking properties, improving overprint ink transferability, and matting.
Although other products are not as good as SIPERNAT ® 820 A in terms of white ink coverage and whitening effect , they each have their own uniqueness, which also determines that they are different from SIPERNAT ® 820 A and can be applied to different requirements.
SIPERNAT ® 833
SIPERNAT ® 833 has better grinding and dispersion properties than SIPERNAT ® 820 A.
We prepare 100 grams of 8% aluminum silicate slurry according to the following formula, and the grinding resin is 30% Degalan 64/12 N acrylic resin liquid (the solvent is n-propyl ester).
The test recipe is as follows:
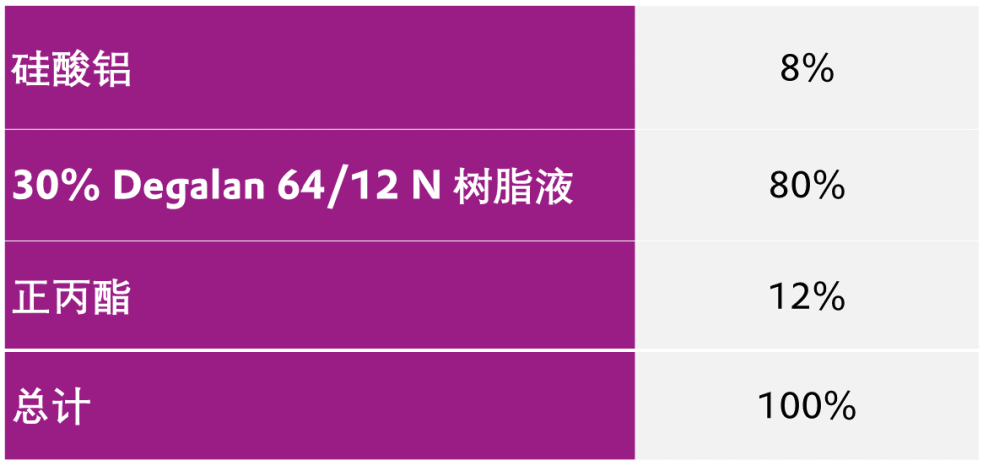
Put the glass beads in and grind with oscillation, and compare the time it takes for the grinding fineness of the slurry to reach <20um.
Figure 1 Comparison of the time taken to disperse fineness of aluminum silicate
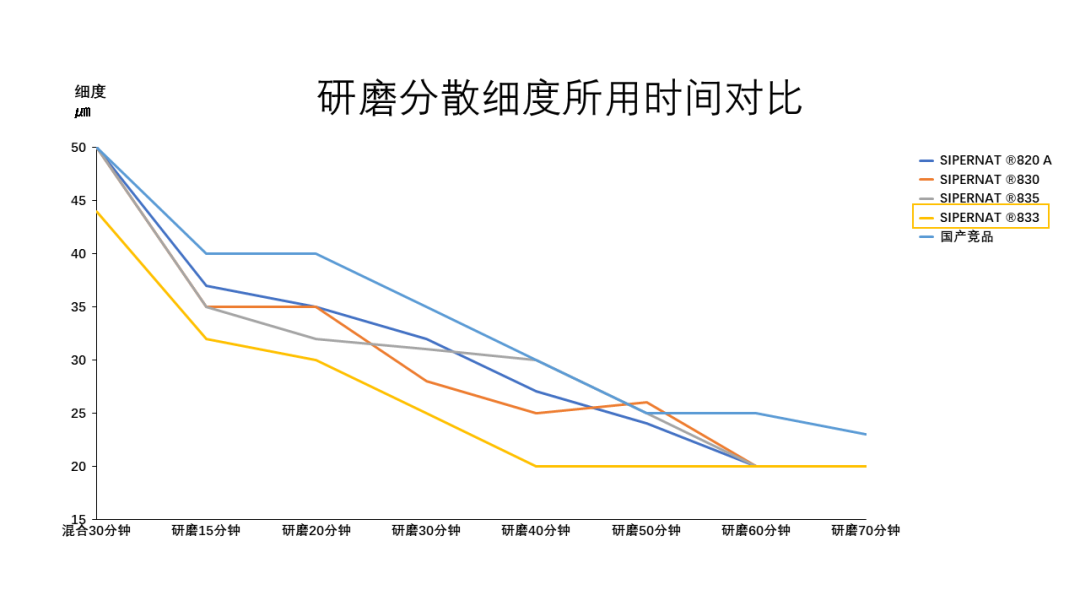
As can be seen from the figure above, SIPERNAT ® 833 is the easiest to grind and disperse, followed by SIPERNAT ® 820 A, and the domestic competing products have the worst grinding and dispersibility.
It can be seen that SIPERNAT ® 833 is particularly suitable for white ink applications that require high grinding and dispersion properties.
SIPERNAT ® 835
SIPERNAT ® 835 has excellent mixing and dispersing properties and is especially recommended for applications that do not require grinding and dispersion but only require mixing and dispersion .
Take water-based printing glue as an example: the original formula contains 35% titanium dioxide, and 4% of the titanium dioxide in the test formula is replaced by aluminum silicate. The dispersion condition is 2000RPM/20 minutes. After testing: the fineness is as follows:
Figure 2 Comparison of the fineness of aluminum silicate used in printing glue
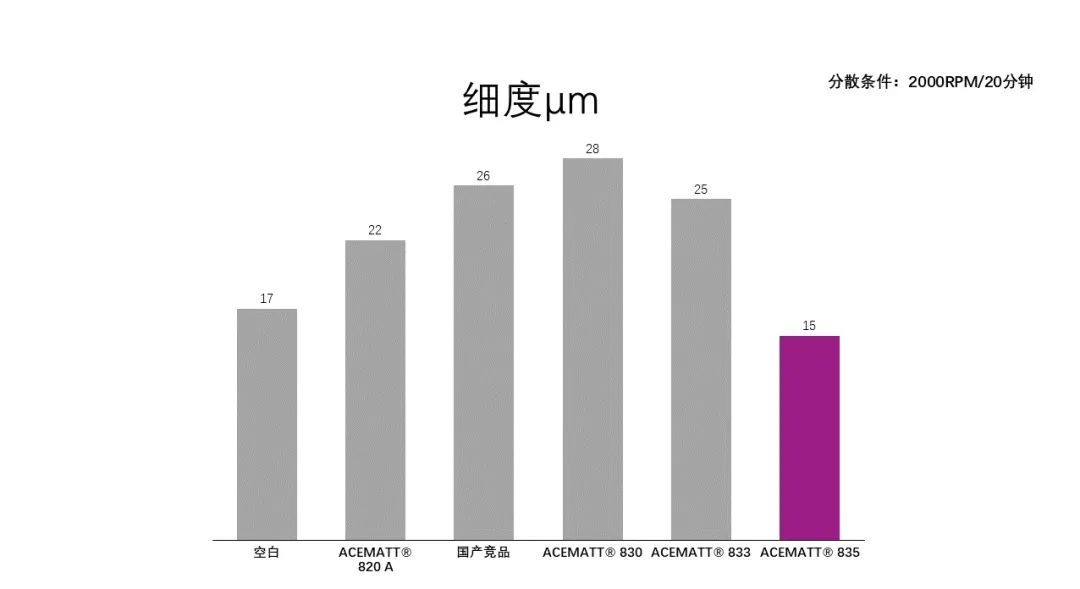
According to the above experimental results, it can be seen that the dispersion effect of SIPERNAT ® 835 is better under stirring and dispersion conditions .
Based on SIPERNAT ® 835's ability to be easily stirred and dispersed, it is also widely used in carton inks or varnishes. It not only provides good anti-slip effects, but also avoids the problem of easy precipitation of traditional filler calcium carbonate.
The following is a comparison of the precipitation of water-based blue ink used in carton inks containing 10% SIPERNAT ® 835 and 10% calcium carbonate.
Figure 3 Comparison of precipitation between SIPERNAT ® 835 and calcium carbonate
(Storage conditions: 50℃, one week)
Figure 4 - Comparison of the dynamic friction coefficient of printing inks after adding SIPERNAT ® 835 and calcium carbonate to carton ink
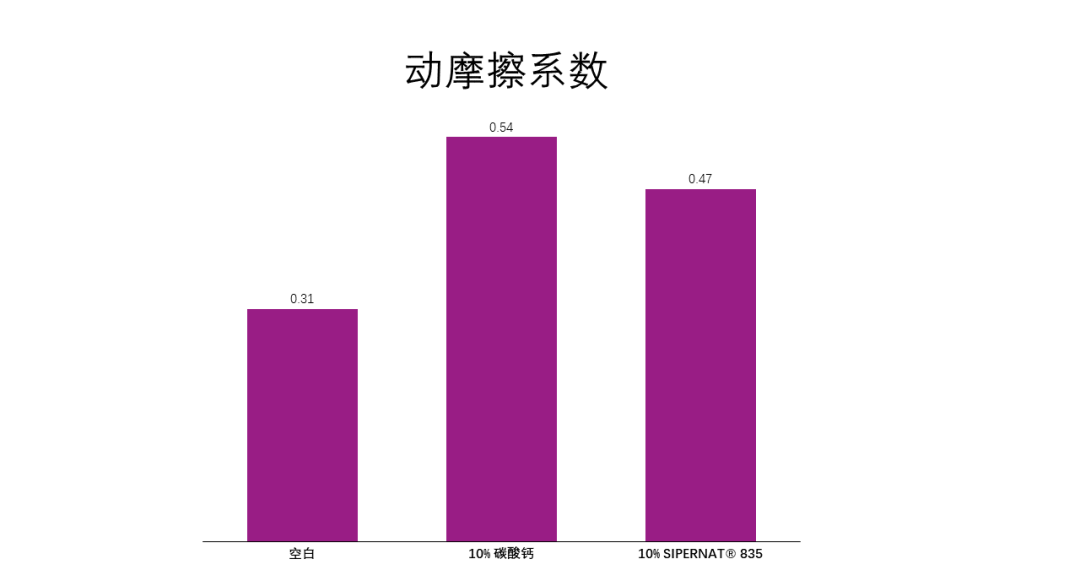
It can be seen that SIPERNAT ® 835 not only has a good anti-slip effect, but also does not settle. In specific applications, calcium carbonate can also be used in combination with SIPERNAT ® 835.
SIPERNAT ® 830 is the product closest in performance to SIPERNAT ® 820 A.
SIPERNAT ® 820 A Frequently Asked Questions
Q&A
Due to the recent skyrocketing price of titanium dioxide, SIPERNAT ® 820 A continues to be a hot seller, and customers have also raised various questions.
Question one
🎤 SIPERNAT ® 820 A is not easy to grind and disperse in white ink.
👨🏫 Considering that the specific gravity of titanium dioxide is greater than that of aluminum silicate, it is recommended to add SIPERNAT ® 820A first and then add titanium dioxide during stirring and dispersion , so that the dispersion effect is better.
Of course, SIPERNAT ® 820 A can also be replaced by SIPERNAT ® 833 , which has better dispersion .
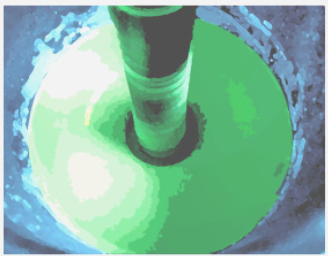
Question 2
🎤 When SIPERNAT ® 820 A is used to improve the transferability of overprinting ink, will it affect the gloss of the ink?
👨🏫 When SIPERNAT ® 820 A is used to improve the transferability of overprinting ink, the addition amount is only 0.3%-0.5%, so it will basically not affect the gloss of the ink.
Question three
🎤 What is the appropriate dosage of SIPERNAT ® 820 A? Why is it sometimes not white?
👨🏫 The addition amount of SIPERNAT ® 820 A in packaging ink is 5%-10 % of the titanium dioxide content , and in printing glue it is generally 3%-5% of the total formula . Since SIPERNAT ® 820 A needs to interact with titanium dioxide to improve coverage, the more titanium dioxide in the formula, the more obvious the effect. Generally, it is better to have a titanium dioxide content of more than 30% in the original formula .
Question 4
🎤 In composite packaging inks, customers often report that SIPERNAT ® 820 A will affect the surface roughness of the ink, thereby affecting the compounding effect of solvent-free glue.
👨🏫 The amount of SIPERNAT ® 820 A can be reduced, and SIPERNAT ® 820 A can be used to replace the matting powder and titanium dioxide in the formula at the same time. This can maintain the film-forming roughness of the ink, thereby improving the white ink coverage and reducing costs. Effect.
Specifically, take the following formula as an example:
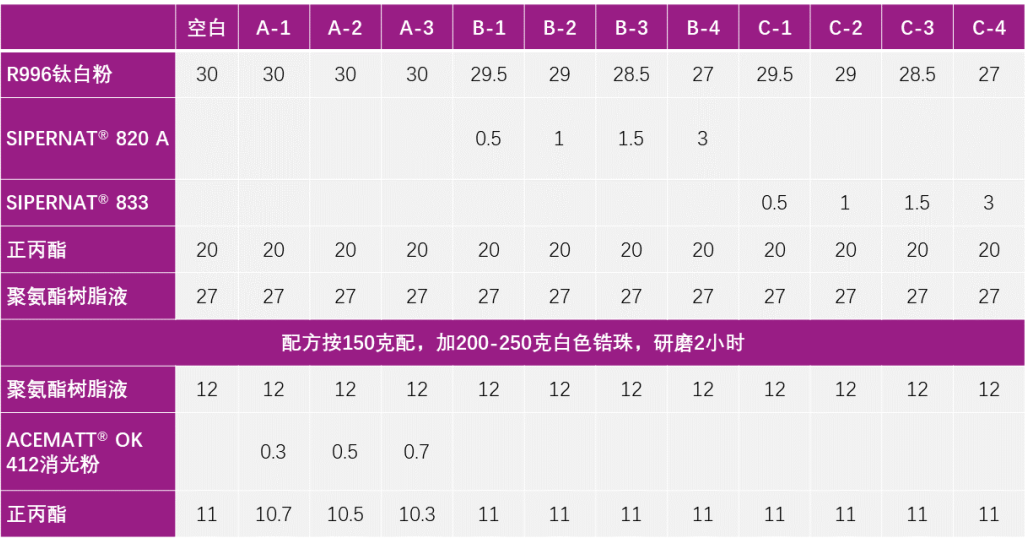
Compare ink gloss as follows (gloss can reflect the roughness of ink)
Figure 5 composite white ink gloss comparison chart
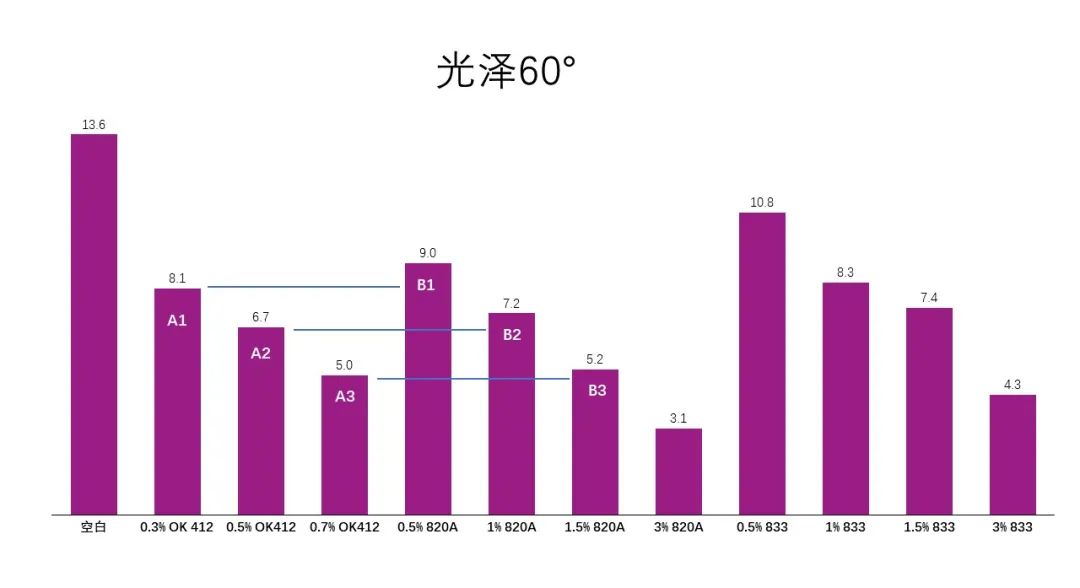
As can be seen from the figure above, the roughness caused by two parts of aluminum silicate is close to the roughness caused by one part of matting powder.
Figure 6 Comparison of coverage rates of composite inks
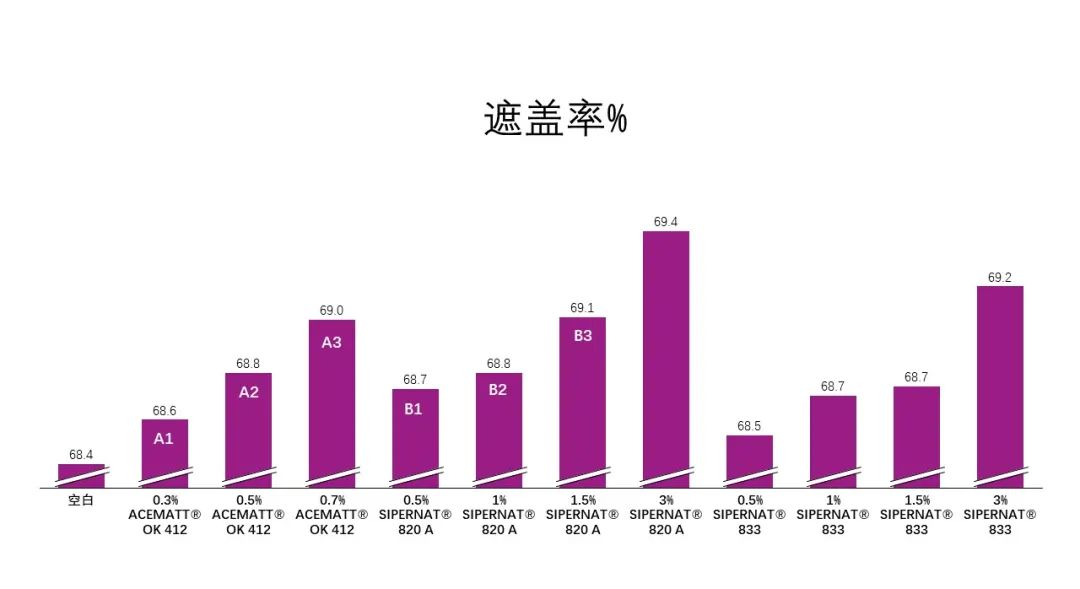
From the above experimental results and comparison of A1 and B1, A2 and B2, A3 and B3, it can be seen that 1 part of aluminum silicate can be used to replace 0.5 part of matting powder and 1 part of titanium dioxide at the same time, which can maintain the original roughness of the ink, and at the same time It can also improve the ink covering rate and reduce the ink cost. Of course, you can also choose SIPERNAT ® 833, which has less impact on the roughness of the ink , but its covering rate is slightly worse than SIPERNAT ® 820 A.