Honeywell Solutions in Non-Cure Rubber Asphalt Waterproof Coatings
Release Time:
2021-09-15
Non-cured rubber asphalt waterproof coating uses rubber, asphalt and softened oil as the main components, and is mixed with temperature control agent and filler to make a waterproof coating that maintains a viscous paste state within the service life. It has self-healing properties and is suitable for construction engineering deformation. The waterproofing treatment of seams and other special parts has outstanding effects, and is widely used in non-exposed building waterproofing projects.
Current implementation standard: JC/T 2428-2017 "Non-cured rubber asphalt waterproof coating"
serial number | project | Technical indicators | |
1 | Solid content/% | ≥98 | |
2 | Heat resistance/℃ | 65 | |
No slipping, running, dripping | |||
3 | Low temperature flexibility | -20℃, no breakage | |
4 | Oil permeability/sheet | ≤2 | |
5 |
bonding performance |
Dry base | 100% cohesive destruction |
moist substrate |
Note: For other detailed indicators, please refer to JC/T 2428-2017 "Non-cured rubber asphalt waterproof coating"
Non-curing construction method
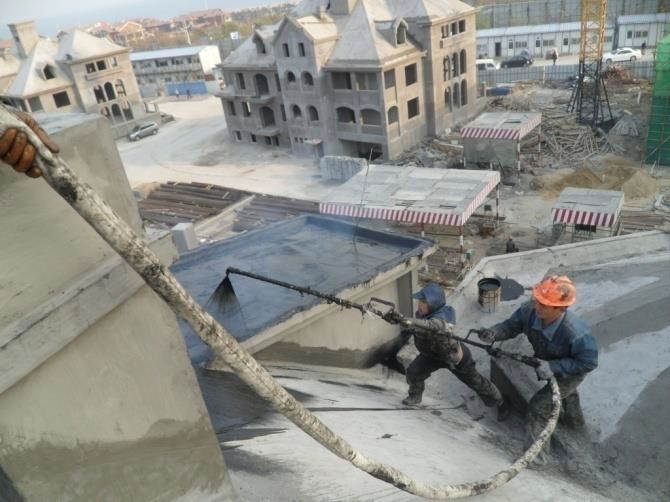
Spraying construction
Scratching construction
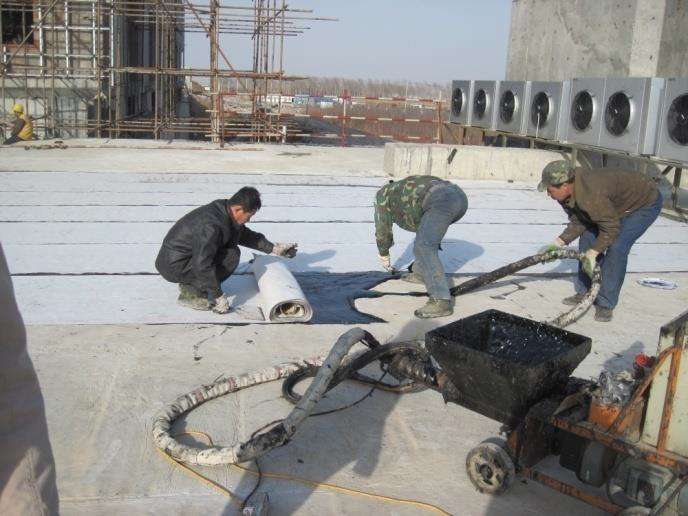
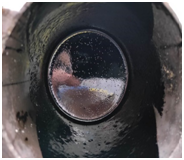
Introduction to Honeywell’s high temperature resistant modifiers and their functions
/ |
Honeywell® RF-1000 |
Honeywell TITAN® 7686 |
---|---|---|
product type |
Homopolyolefin |
Oxidized polyolefin |
The essential performance |
Significantly improves heat resistance by 2% The dosage is heat-resistant through 75 degrees |
Significantly improves heat resistance by 1.5% The dosage is heat-resistant to 90 degrees
|
product application |
Meet or slightly exceed the national standard |
Leading the national standard, Xiongan standard |
The role of Honeywell high temperature resistant modifiers in non-cured rubber asphalt waterproof coatings
✦ Increase softening point and improve heat resistance
✦ Reduce penetration
✦ Reduce viscosity: increase production line speed; reduce processing temperature; increase filler dosage
✦ Reduce oil leakage
✦ Improve the wettability of the fetal base
✦ Improve adhesion
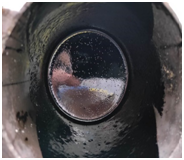
Honeywell’s main product technical indicators and main features
/ |
RF-1000 |
Test Methods |
Melting point/℃ |
113 |
ASTM D-3954 |
Penetration (25℃) |
<0.1mm |
ASTM D-5 |
physics form |
Granular 100% Pass 30 mesh screen |
/ |
RF-1000 is a new high-temperature resistant additive for asphalt that meets customers’ requirements for improved temperature resistance while providing reliable quality stability and high cost performance, thus reducing the total cost of using high-temperature resistant additives.
◆Help customers develop new non-curing waterproof coating products that meet or exceed industry standards
◆2% dosage can increase the softening point of asphalt by more than 15℃
◆Reduce the viscosity of the asphalt mixture to facilitate the spraying construction of non-curing asphalt coatings at lower temperatures (such as 130°C).
◆Stable supply and short delivery cycle.
◆Recommended dosage: about 2% of the total weight of non-cured asphalt coating.
characteristic |
index |
Hardness--25℃(77°F) |
<0.5DMM |
Dropping point |
136℃ |
Acid value |
25MG KOH/G |
150℃ viscosity |
4500CPS |
density |
0.99G/CC |
Product advantages
◆Greatly improve the high temperature performance of asphalt coatings.
◆Does not affect viscosity level and facilitates production and construction.
◆Good compatibility with asphalt, no segregation, and good appearance when opening the can.
◆Recommended dosage: about 1-1.5% of the total weight of non-cured asphalt coating.
Honeywell high temperature modifier test data
Recipe composition | Add scale | Raw material model |
Base bitumen | 42% | SK70# |
Naphthenic oil | twenty two% | Sinopec |
SBS | 2.50% | Sinopec 1301-1 |
SBR | 2.50% | Shandong Gao's |
talcum powder | 28% | Generally available on the market |
/ | 98.5% | / |
formula | 130℃ viscosity | Softening Point | heat resistance |
Basic recipe | 1600 | 51.5 |
through 65℃, Failure at 75℃ |
Basic recipe +1.5%HON 7686 |
1500 | 80.3 | Pass 90℃ |
Basic recipe +3%RF-1000 |
1400 | 84.2 | Pass 90℃ |
Basic recipe +2%RF-1000 |
1430 | 77.8 | Pass 75℃ |
Basic recipe +1.5% domestic oxidized wax |
2500 | 79.1 | Pass 90℃ |
in conclusion
✦2% RF-1000 can increase the heat resistance by 10 degrees and reduce the viscosity of the formula system.
✦Increase the dosage of RF-1000 to pass the 90 degree heat resistance test.
As Xiongan New District further clarifies the heat resistance and viscosity of non-cured rubber asphalt waterproof coatings at 130°C, it will develop towards high heat resistance and low construction temperatures. The selection of high temperature resistant modifiers is crucial to improve Softening point, lower viscosity at high temperatures, and lower use of naphthenic oils will improve the quality of non-cured rubber asphalt waterproof coatings.
Modifier type | Typical indicators |
Honeywell wax |
RF-1000 melting point: 113℃ 7686 Dropping point 136℃ Viscosity at 150℃: 4500CPS |
Domestic oxidized wax |
Acid value: 10-40MG Viscosity at 150℃: >10000CPS |
PP wax |
Melting point: ~160℃ Viscosity at 170℃: ~300CPS |
Domestic polyethylene wax |
Melting point: ~110℃ Viscosity at 140℃: ~500CPS |
EBS | Melting point: ~140℃ |
Modifier type | Performance characteristics |
Honeywell wax | Significantly improves high temperature performance, reduces system viscosity, and lowers construction temperature at the same time. Good compatibility with asphalt, no segregation problem |
Domestic oxidized wax | It can improve high-temperature performance, but increases viscosity, making construction inconvenient and product stability not high. |
PP wax |
It can improve high temperature performance, but it dissolves slowly, has poor compatibility, increases viscosity, is inconvenient for construction, and reduces the bonding performance of the system. |
Domestic polyethylene wax | Limited improvement in heat resistance |
EBS | Limited improvement in heat resistance, easy to precipitate, affecting the appearance of the can after opening |
The heat resistance and viscosity of non-cured rubber asphalt waterproof coatings in Xiongan New Area are specified as follows:
item Head |
unit | Reference value |
testing base |
Resistant hot sex |
℃ |
≥90 |
JC/T2428-2017 7.9 |
stick Spend |
MPa·s | ≤1500 |
Tested in accordance with T0625-2011 in JTG E20-2011* |
*Note: Test temperature is 130℃. Before the test, select a rotor with a torque in the range of 20%-80% based on the viscosity result of the sample being tested. During the test, wait until the temperature of the material stabilizes before testing.
Corresponding solution: Honeywell TITAN® 7686 is selected as the high temperature resistant modifier, and the recommended addition amount is 1.5%.